Fanuc 31i Mb Operator Manual
The Series 30 i/31 i/32 i-MODEL B CNCs are designed for today’s most complex, high-performance machines with a large number of axes, multiple part program paths and high-speed auxiliary machine functions. The Series 30 i-MODEL B supports up to 32 servo axes, 24 simultaneous interpolated axes, 8 spindles and 5 independent PMC machine ladders. The Series 30 i/31 i/32 i-MODEL B CNC is ideal for your next machine, whether it is a simple lathe or mill, or the most complex part profile, multi-axis application. 5-axis machining with Series 30 i-MODEL B and Series 31 i-MODEL B5, for precision parts that faithfully match the original CAD drawing, with faster cycle times, improved surfaces finishes and simplified part programming, setup and operation. Mill-turn and 5/6-sided machining, combining turning and milling in a single part program to reduce setup and cycle time and improve quality. Linear and rotary transfer machining for the shortest cycle times for high volume manufacturing with the convenience and simplicity of a single CNC interface for multiple spindles and stations. Precision grinding, with the performance and accuracy for cylindrical, surface and profile grinding.
Gear cutting, synchronizing multiple axes and spindles and providing highly customized operator interfaces for high quality cylindrical and bevel gear machines. Woodworking machining of large nested part programs at ultra-high speed while maintaining accuracy for flat-bed and 5-axis routers. New processes and technologies that require high performance motion control in applications such as composite tape laying, riveting, water jet, laser, friction stir welding and EDM. Available on the world‘s best-in-class machine tools Available on the world’s leading performance machine tools including multi-axis lathes, 5-axis machining centers, gear cutting machines, transfer machines and state-of-the-art, non-traditional applications. Ultimate resolution and precision for quality machining The CNC and drive system executes at a nanometer resolution all the way down to the 16-million count encoders for the maximum precision and the smoothest contoured surface finish quality. High-speed machining for quality and reduced cycle times Advanced software algorithms analyze part geometries and machine capabilities and adjust trajectories and feedrates to provide the smoothest tool paths for the highest processing speed at the specified precision.
Simple operation for maximum productivity Operators with previous FANUC experience can use their existing skills as they learn new techniques, and existing part programs will run smoothly with little or no modification. Connectivity for today’s high-tech manufacturing The 100-MBit Ethernet interface integrates the CNC into a network for high-speed part program transfers and the collection of process related data. It also supports remote troubleshooting from the maintenance department or a machine tool builder anywhere around the world. Because the Ethernet port does not use a public operating system, it is practically “hacker-free” and virus immune. High reliability and easy maintenance Reliable hardware with clear diagnostics provides a stable platform for maximum machine availability. With a mean-time-between-failure of up to 52 years, and production lifetime product support, FANUC controls provide machine availability that far exceeds any competitor. Powerful simulation tools Simulation of CNC operation, part programming and maintenance screens for effective training of operators, part programmers, maintenance engineers and technicians in a safe environment.
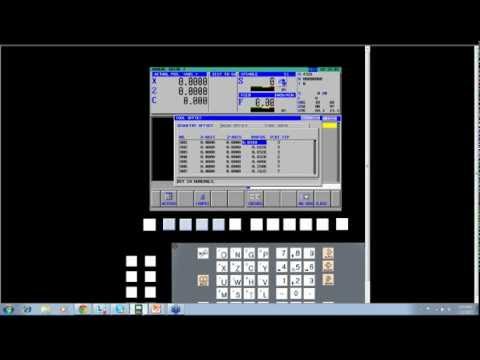
State-of-the-art hardware Ultra-high-speed processors provide fast interpolation times with up to 1000-block look-ahead, controlling up to 10 paths and 40 axes, up to 24 axes simultaneously. Up to 5 independent, 9.1 nanosecond-per-step PMC ladders execute simultaneously, supporting up to 4096 digital inputs and outputs.
Customer-specific solutions Unique solutions may be realized using powerful programming languages, user-interface development tools, real-time macros and PC functionality. The Series 30 i, Series 31 i and Series 32 i CNCs may connect with Windows compatible PCs, or rugged, diskless Windows CE.NET operator interfaces.
The Fanuc Series 31i is part of the interchangeable control WinNC. WinNC allows the user to learn all CNC industry controls that are common on the market on a Concept machine or on a programmers place. One of these controls is the Fanuc Series 31i. It corresponds in terms of handling and function to the particular original control and it can be used on a PC.
The user has the possibility to work on the PC as well as on the machinecontrol and gets familiar with all aspects of control programming in detail. The WinNC Fanuc 31i includes Manual Guide i work-step programming. Win3D-View is a 3D simulation for turning and milling and is available as an option in addition to the WinNC Control. Graphic simulations of CNC controls are designed especially for industrial experience. Win3D-View displays exceed industry standards. Tools, blanks, clamping devices, and work processes are highly realistic.The system checks the programmed travel of the tool to prevent collision with clamping devices and blanks.
If there is a conflict, a warning is given so that manufacturing processes can be understood and controlled from the very beginning. That's the aim of Win3D-View: Visualizing, supporting and avoiding costly collisions. “Easy2control” adds a range of attractive applications to the successful interchangeable control system used in EMCO training machines.
Suitable for use in machines and simulation workplaces alike, it displays additional control elements directly on the screen and, when used together with a touchscreen monitor, provides the ideal input interface. With support for a wide range of keyboard variants, customer-specific screen layouts and tailored solutions for individual customers, Easy2control represents a promising and highly flexible extension to the modular EMCO training concept. The interchangeable controls are represented using an on-screen keyboard, which makes switching between different control systems even easier and quicker. The DNC-Interface (Distributed Numerical Control) allowes a remote control of the control software (WinNC) via a software-protocol.
The DNC interface creates a connection between a superordinate computer (production master computer, FMS-computer, DNC-host computer etc.) and the control computer of an NC machine. After activation of the DNC operation the DNC computer (Master) takes over the control of the NC machine (Client).
The entire production control is completely assumed by the DNC computer. The automation devices such as doors, clamping chuck (collet), sleeve, coolant etc. Can be controlled by the DNC computer. The actual status of the NC machine is displayed on the DNC computer. For more information about DNC, click here. CAMConcept is innovative software for complete CAD/CAM and CNC training, from design to manufacture.
Fanuc 31i B5 Manual
CAMConcept incorporates both the functions of a professional CAD/CAM system and the advantages of a special training program for machining technology. All core CAD program functions are available. Graphic displays of CNC cycles allow quick programming, while simulations and collision checks ensure that control programming is safe. The 3D simulations make it perfect for training at programming stations, and also for making complex turning and milling workpieces simple to produce any time. With its many functions, user-friendly operation and clear structure, CAMConcept is one of the leading software systems in the field of training.